First you have to grind the area until you think you have gotten the strike out, then polish it with a 120 Grit (or finer) sandpaper. Look at it with light from different angles. Sometimes the hard spot can actually be seen visually. Most times, you have to grind about 1/32 inch or more to get rid of the phase change area under the site of the arc strike. Arc Strikes on cold material are worse than arc strikes on hot material. You have to be carefull, because often the minimum thickness is such that very little grind out can be tolerated.
Amonium Persulfate solution should be mixed at a rate of 20% granular Persulfate to 80% pure water by WEIGHT. Unless you have a good sensitive electronic food scale, you should use a postage scale or a re-loaders powder scale. One gram of persulfate is less than a teaspoon. 4 grams of water is not much either. You need a very small water tight container with a plastic lined inside top. Keep the solution out of the sunlight. This solution can be carried around in your car without danger of fire or explosion. If the cap vibrates loose, it will rust your car wherever it splashes! You can dip your finger in it and you will not get burned.
I recommend you apply it with a Q-Tip. The solution works fastest on a carbon steel surface that is between 120 and 150 degrees F. This solution does not work with austenitic Stainless Steels. (Arc Strikes are less imnportant on those materials anyway.) You need fresh water to neutralize the action after you develop the indication. Bottled water is fine. If you wipe the area with a rag, you may smear grease or oil and that will obscure your indication.
It is good "Show-and-Tell" to do the polishing and developing of the indication in front of the welder. So many of them think that arc strikes don't mean anything.
WOW.
The info on persulphate is interesting,and certainy of value. But don't ya'll think that worrying about phase changes, 120 grit, light from different angles in carbon steel is a bit overreacting in most instances? Unless there is some specific requirement otherwise?
Wouldn't an MT or PT checking for cracks be more reasonable?
The only time we ever run into this level of attention is when dealing with gas transmission lines. Given that most transmission line owner/operators expect these lines to be there "forever", it still seems heavy handed, but not that heavy handed.
The real message that needs to go out to the welders is to eliminate arc strikes outside the weld. That is always the best message, but when they see just how seriously some owners are, their attention to detail improves drastically.
Charles.
Charles, I appreciate the info on the persulphate. The thought occured to me to utilize it myself in some manner, especially for HSLA's and the like.
But in total agreement with you, I had no intent of implying that arc strikes do not need to be taken seriously. It just that in som alloys they are more serious than others.
I neglected to add, that I have often been required to perform hardness tests on the spot during and after the removal. It is an interesting and revealing operation. When just ground flush, the spot is often less than RC 18. Then you grind a little bit more, and check the hardness again and it goes up to RC 34 to 42. Than you grind and polish it deeper and when you finally get it out, it is les than 18 again. I have done this during D 1.1 Inspections just to show the welder that he hasn't removed the Arc Strike!
Joe ,
Correct me if I am wrong but are not arc strikes considerd a failure of the weld as a whole. At least in all the tests I have ever taken that has been the case. If in fact the welder does not consider this to be so, how did he get into the position of having todo a pressure weld to start with? I would like to read the code that says you can grind them out. If you could post that I would like to look it up.
Hello makeithot, you have a valid point when you say that any test you ever took would not allow any arc strikes outside of the weld joint on a pressure test and as well on many other types of certification tests. Having that occur during the test is an automatic failure in many cases. You also know that in the real world situation there exists the possibility for arc strikes to happen outside of the joint even when the best precautions are taken. I have read other threads that have discussed this at length and it appears that for the given codes that apply to various situations, there are allowances and procedures for the repair of these occurences. As one of the posts on this thread suggested, when the grinding, polishing, and etching showed that the imperfection was gone but the thickness limits were compromised, this was justification for a cut-out, if the material still had the proper thickness intact, the repair could be accepted. Just my take on this. Regards, aevald
I think the danger of arc strikes, as I suggested in the previous post varies with alloy. For carbon steels I don't know that there is much justification in documented failures for consideration beyond cracking.
However, using hardnesses to demonstrate to welders the effect of arc strikes, even on carbon steels is a excellent idea.
From all that I read in books, regular carbon steels are not supposed to be bothered by accidental arc strikes. But I have seen that little hard spot many many many times. I have also seen the little dot caused by an underbead microvoid coalessence (presumably caused by the arc strike), after the arc strike had been ground down considerably!
On one pipeline that I saw, the Brooklyn Union Gas company had a requirement in the late forties and early fifties, that all welders had to weld their mark next to each joint that they welded. One Guy had a big flourished signature, welded near everyone of his joints . "E.VanDaly" had a signature that would give John Hancock a complex.
In the middle 90's, the gas company decided to get rid of all the old spiral wound pipe, because they didn't trust it for MAOP that they wanted to get, so they dug it all up and replaced it with straight seam pipe. There were Arc Strikes all over this pipeline and it never blew up due to arc strikes and John Hancocks!
As an inspector on a pipeline project, I allowed the fitter to leave small pin punch marks (low stress), (used for alignment, during fit up,) on the pipe. The NYS Public Service Commission told me I was not allowed to permit those pin punch marks to remain. I had to treat them like Arc Strikes and have the contractor remove them. The rules also said that the fittings (Els) had to be marked with Low Stress Markers. The manufacturers also had High Stress markers on the opposite side of the same piece, but the PSC didn't care about that!
I do not know about failure of the weld as a whole. (If you meant "Whole") If youmeant "Hole", I do have a series of film slides showing a burn hole completely through on the weld metal on a pipe joint caused by poor contact of the "Antler" grounding device on a 16 inch Cross Country pipeline.
As Mr. Hall points out, mostly, I have seen the Amonium Persulfate requirement in Pipline work. The State Public Service Commission Rules and Federal Pipelins safety rules required this type of handling.
However in NYS Bridge work, the New York State Steel Construction Manual requires hardness tests for all arc strike removals.
CON-ED also required it for proof of Arc Strike removal on the inside water wall of their power generation boilers. If you left an arc strike on the water wall tubes they would burn through in less than a week in some areas of the near impingement zone.
I was up on the Alaskan Pipeline in 1974, and the welders were only allowed to have two arc strikes in their lifetime, before being sent down to the lower forty eight. They had to go back through the Oklahoma Pipe Welders school before they were allowed back on the job. (I was not there as a welder, so I did not understand the significance of this at the time.)
Should have spent more time learning how to speel. What I meant to say was "whole" not "hole"

Speaking of "show and tell"...
I laid several pieces of 3/8" flatbar x 2 out on a table side by side and had one of the welders drag a 7018 across the flatbar pieces really quickly, and then had the welder grind them out to his satisfaction. I bent them in my coupon bender and here is what I showed him....(the piece without the cracking is the clean piece to show the welder that it wasn't the material becaause they were all cut from the same flatbar.)
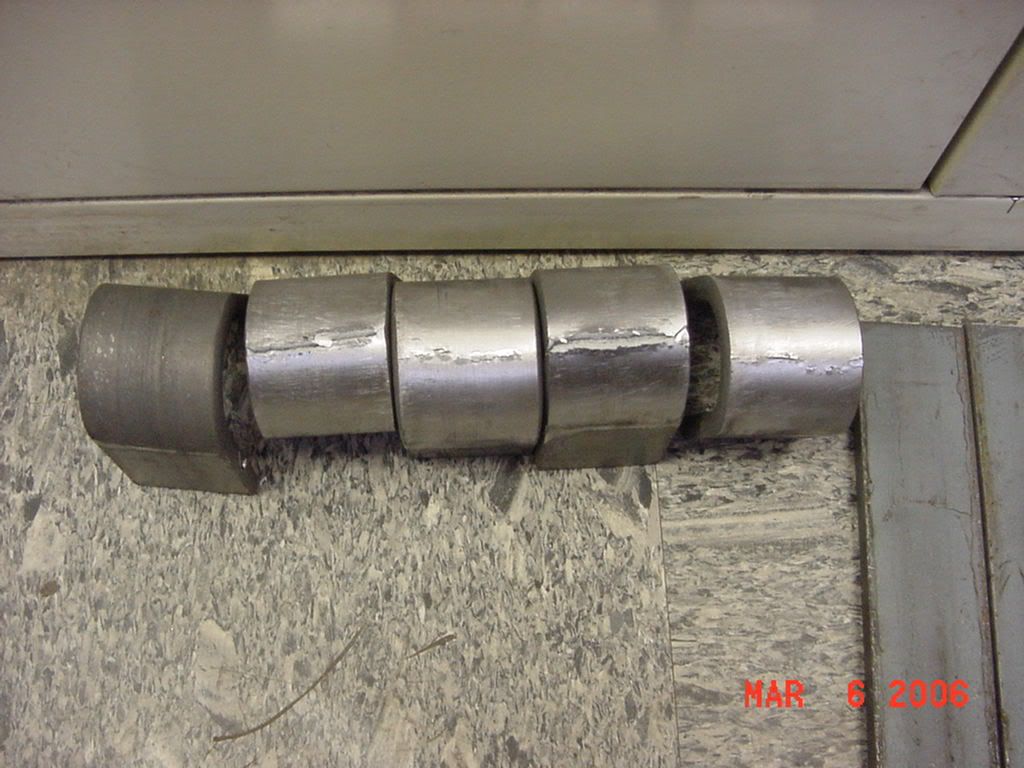
and a picture up close....
Hello John, nice pics, definitely show the stress riser effect that could lead to failures. One comment I would like to include here has to do with weld identification by welders on gas transmission lines. One of my welding instructors spent a considerable number of years working for Pacific Northwest Natural Gas, when he first started welding for them they required all welds to be stamped by the welder with his personal stamp. He said that not too long after that they discontinued the practice when they started noticing that many of the pipe failures that they were having were due to the impressions made by the stamps. My $.02 Regards, aevald
I have seen that example once before when I started out as an apprentice. Nicely done. I feel that it reinforces my belief that an arc strike would be cause for concern testing or other wise. Brings me back to my original question " Is there an actaul written code for repiar of arc strikes " If so where? Or is this normally left to the clients discreation as to what is considerd aceptable.
Search the CFR: 10CFR49 subsection 192.309: Repair of Steel Pipe. An arc strike is called a dent, and must be repaired if certain limits (defined) are met.
10CFR49 192 is applicable only to gas transmission systems. Someone else will have to chime in for other components.
Charles
makeithot,
I think in answer to your question, there is mention of 'repairing' arc strikes in virtually all construction codes in soime manner or another. Some more stringent than others. Most codes will write it as a minimum standard in recognition of the fact that the concern for arc strikes is very alloy and service dependent.
TO: jwright650
I teach welding tech at the high school level. I have heard of this experiment several times but never tried it. I saw your pictures and decided to try it with my advanced class that is getting ready to do state certifications. I took 4 pieces of 1/2" x 2" flat bar 6" long and we bent one as a control (which bent perfectly). I had a student drag a E6010, E7018, and MIG across the other samples, we then ground them down and buffed them to a good appearance and bent them in our guided bend tester. The results were exactly like yours. It was an excellent demonstration of the effects of arc strikes. Thanks!!!
I have seen the effects of arc strikes in RT and UT in industry but this is an excellent, simple demonstration that gets the points across.
Joe, just an FYI-
I recently used ammonium persulphate to detect when some unauthorized welding had been completely removed from a bridge girder bottom flange. It worked very well as far as contrasting weld metal against the base metal.(Some scrap angles had been welded to the top of the bottom flange to serve as a temporary brace for drain scuppers. Naturally, that earned some very negative atention from the DOT. I was asked to help resolve the problem.)
I do not disagree that taking the care you described is a good idea to get consistent and predictable results. However I did not have much available under field conditions, let alone any types of scales.
I simply poured some granular ammonium persulphate into a new plastic spray bottle and added tap water until I had what I approximated to be a 1 to 10 ratio. I tested the solution on a sample I had made up. Temperature was around 60 degrees F. Having read over some very explicit instructions on how to mix up and apply the solution, I had some apprehension about it, but it worked fine on the sample.
We used a flapper disk on a 4" grinder which gave a very smooth finish. Being a girder flange, the idea was to remove the absolute minimum needed to "make it go away". we sprayed on the solution and found that it was important to keep the treated area wet - spraying a bit more as the area dried out.
It took about a minute to actually see the contrast develop, but when it did the weld metal was clearly differentiated from the base metal. When the solution dried out, a quick spritz made it jump out again.
We were in a man-lift, on a barge and chemicals getting in the water was a concern, so we kept rags around and under the test area to capture any drips and run-off. and also the rinse solution which was tap water in another spray bottle.
To conclude- the areas were measured as reducing thickness no more that 0.035", the flange was actually 0.025" average greater than the specified thickness, RT was done on all areas, so DOT was OK with leaving the repairs as is.
Hi Chet
Now I understand why you sprayed it.
As for the exact mixture, it actually has a pretty wide operating range in dilution with water. However, if you go too rich or too lean, it doesn't work at all. This is a good example of how good this etchant is. I don't know why you had to protect the water in the river. I bought my bottle of Amonium Persulfate from Fischer Scientific about 20 years ago. (At that time they would sell to individuals). The literature at that time, said it could be disposed of without any hazard precautions. I can also recommend a faster acting etchant, that works in any temperature. Ferric Chloride. I obtained my Ferric Chloride from a Sewage Treatment plant. They used it in the Water Purification process, so I believe that it can also be disposed of in the river.
I sure would like to know how the DOT discovered that the fabricator had used the temporary attachments welded to the flanges! Where was the inspector!?!? What DOT was involved?
Joe,
There were some overall environmental concerns with an endangered species that made it much easier to prevent anything from going into the water, rather than try to explain why no harm would be done.
As far as the mixing ratio, I guessed at it but that was why I used a sample to test the solution on. The DOT was on hand to witness the testing before we used it on the bridge- and they witnessed the actual work. Incidentally, I did consider trying to measure the hardness as a means of differentiating weld/base metals but I only had a portable identing tool with microscope (PTC Instruments) and found that everything was less than a RC20. Weld metal and base metal gave below scale readings.
What makes you think a fabricator was involved? :) Actually, it was a field mistake, the carpenters didn't want to wait to brace off the scuppers when they were forming up the deck. Big oops. I was asked by the DOT to help resolve the situation. I'm not sure I can divulge the location but it was at least a 7 hour drive one way.
so tell me Charles , this "ammonium persulfate".........what is its primary purpose.....? was this developed for this reason alone , or is it something that just happends to work......?
and thanks for the pics John,,,,,i got to work today,,,,dragged a welding rod across a peice of 3/8th,,and pounded it over,,,,,same thing....ripped it right open..........i would have never believed it............thanks again John........