
This whole thing started as an upgrade in my 1970 braking system. I modified the front spindles
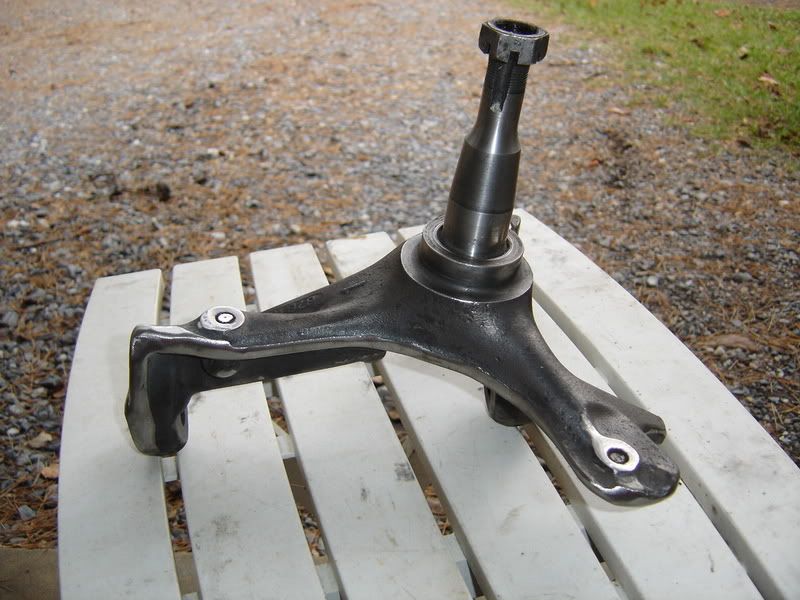
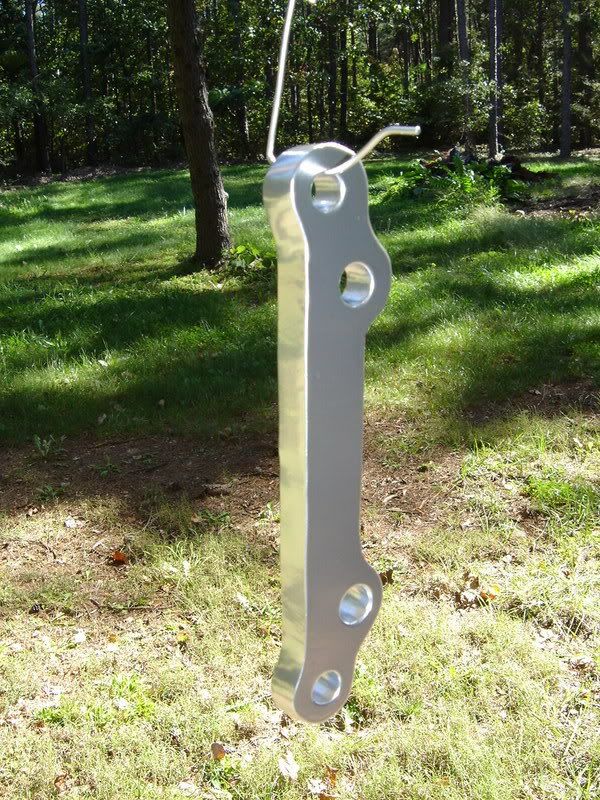
and adapted C5 Corvette calipers to the front and made brackets to hang the calipers on the rear
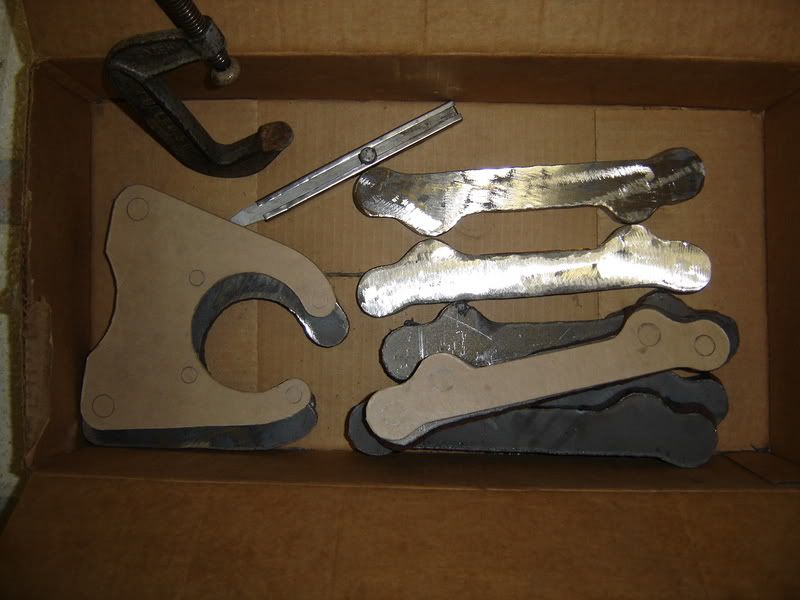
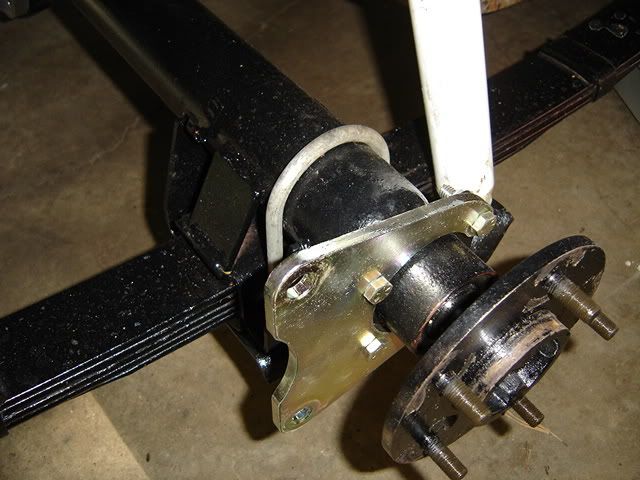
and used the Corvette rotors which are 12.8" in the front and 12" in the rear.
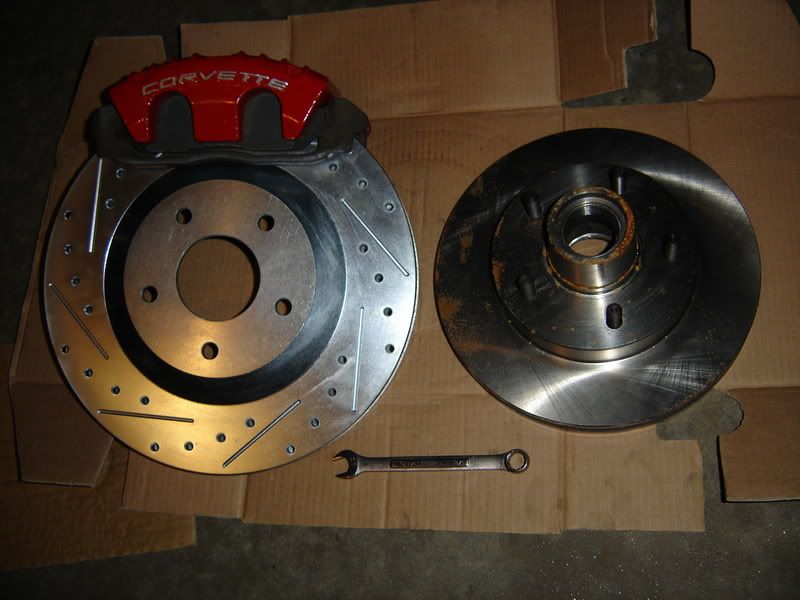
After all this was ironed out, the 15" Z28 five spoke rims would not go over the calipers. So I moved up to a 17" rim. The 17" rim from Cragar is the Soft 8, and doesn't come in widths to accommodate a 315/35/17, but the 9" rim has the correct offset and I was planning to just add 1.5" to the backspacing to make the rim 10.5" wide to accept that large tire.
But for now, I have 275/40/17's on the 9" rim on the rear, and 255/40/17's on the 8" rim up front.