Jim,
Well if it's magnified, that is not the true size.....but considering the size of magnetic particles, I would think that any accumulation could be considered magnified. In Kip's post (regarding MT), it sounds to me like he is just pointing out that excessive powder can make an indication appear wider than it actually is. A perfect example is something we've all seen.... a hairline crack which has been collecting grinding dust in the shop for days. They almost look like they are growing fur. This first picture shows a toe and plate crack where, because of limited access, I have to depend on residual magnetism in the part to hold the dust. These indications are always wider than the actual crack.

These next cracks on the other hand, are very tight and I used a puffer to blow away the excess dust. They are slightly wider than when you view them under a microscope, but due to the particle size that is the most accurate display I can get unless I switch to wet visible or wet fluorescent particles.
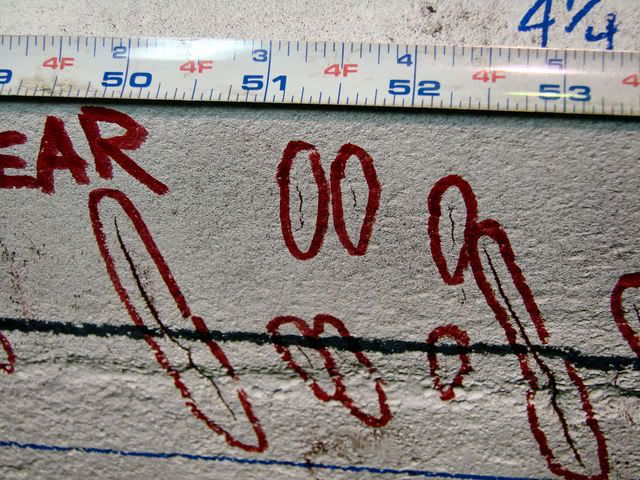
Contrast is something else that works in the inspectors favor, and that's why I selected yellow dust for the red-iron background and red dust on a contrast painted background.