
Does anyone make a ceramic backing (2" x 2") with this recess already cast into the backing?
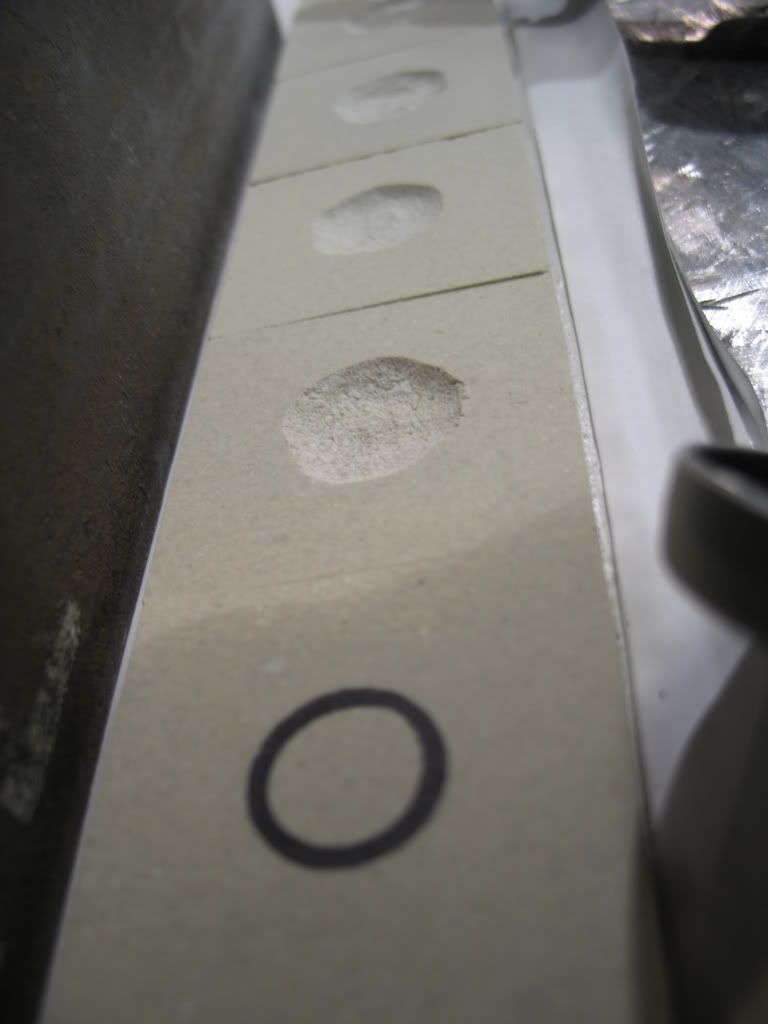
I have been taking a template and a sharpie, marking the ceramic backing.
Then Taking a die grinder and hogging out the center......
....so that when you plug a hole in a piece of plate you have reinforcement built in so a quick grind is all that is necessary...no extra filling.
Sorry John, I can't resist, but apparently you make such an animal! Seriously, I haven't seen such an item commercially available, maybe this is an opportunity? Best regards, Allan

Allan the effort and time to mark and die grind these pieces of backing seems to offset the grind and touch-up welding that we were doing, so I may keep at for a while until I can find some of this stuff already made....now if the holes were punched correctly in the first place, we wouldn't have even had the need for "such an animal"...but as you know sometimes there just isn't enough time to scrap the plate and do it over, so we make do with what we have...uggh.
John, I've always just used the flat ceramic and planned on touching up the other side. I'm curious about how much of the touch-up did you eliminate by recessing those ceramics? I assume it must be significant or else you wouldn't bother but can you quantify that? Thanks.

I'm not totally sure Chet how to quantify it...but when you have to add some material back you can't just squirt a little in, so the reinforcement adds the needed material. It has sped up the grinding side of things.
OK, my question, barring finding a source pre-made the way you want, could you use the proper style (for ceramics) drill bit to put a slight recess in the 2X2 tile? Yes, the operator would have to be very gentle, but it might prove faster than a die grinder. I may have to try that one myself. Good idea though for getting a one sided weld to repair a misplaced hole. Of course, we never have that problem in my shop. HA!! LOL!!
Have a Great Day, Brent

Good idea Brent...we'll have to look into your suggestion...
interesting, could you not use a spacer or washer instead of grinding out the tile? seems like similar results could be accomplished by sandwiching a spacer, not to mention the saved time of grinding out the tile.
still though very ingenious.
Do you have to use ceramics?
One of my co-workers has a 3/16thick 4"x4" square of copper with about a 1.5" dia, 1/16 deep cavity machined into it made just for plugging holes if need be. its reusable compared to the ceramic squares.
Or is copper pick up a problem?
PlasmaHead2,
Copper works well for many things but there are times where the copper pickup in the weld can cause problems. The other factor with copper is trying to get the copper off if the operator doesn't manipulate the arc properly. Depending upon the size of hole, thickness of material, and arc manipulation I would challenge you to get that copper piece, that doesn't weld to steel, off short of air arc or grinding. The bond will be such that even a large sledge hammer and wedges won't break it loose.
It isn't really a trick of the trade, just common sense, but if you keep your arc focused on the edge of the steel and let the molten metal flow down and rest on the backing it won't be as prone to dig in to the backing and bond it.
Have a Great Day, Brent
I just meant what percentage of holes now only require grinding?

I still get one or two out of a group of six that for some reason looked like they had a slight recess to fill on the bottom against the edge of the hole. We figured out that it was the same place where he would start...so something was wrong, but we didn't quite figure it out. Played with the welder, turned it up and down but it never fixed it entirely, even deepened the recess to see if that made a difference.
There are six holes per plate that need to be plugged. We finished all of them yesterday, so I don't have any more to experiement on at the moment.

Hi Guys,
I spoke with the company who makes these ceramic tiles yesterday and explained what I was doing. He said that he would mess around out in the shop and work on his shrinkage rates and see if he can come up with something. I mentioned that you guys may be interested in this as well. So I'll call him back and see how he is making out.
Marsh Ceramics was bought out and the new owners now call it Welding Ceramics...new phone# 423-752-5740
hi john, i just use a grinding wheel to keep weld from falling out, fill the hole, grind, flip plate over, cap back side and grind smooth
This may or may not help but you can also use a "electric motor brush" for this purpose" . The brush is easier to shape but in the size it looks like you may need they may be hard to scrounge up or too expensive to purchase.
HTH
Griff
when I worked in the shop, we hammer the copper bar with the "ball" of the hammer to shape it. that way we have reinforsment on the other side, no grinder need it.
Ive always used brass for a backing plate. When done I have never had trouble removing or the brass mixing with the steel. Ive plugged holes, built parts up with them.
Can you use graphite (carbon block) instead?
You can partially drill whatever size hole in it and use it over.
Very cheap at McMaster Carr.

I'm not sure...that kinda goes along with what Griff had suggested.
I could be wrong, but similar to carbon arc gouging, couldn't there be issues with carbon pickup?
essentially any refractory, or non consumable backing could be used. I guess it's a matter of what's cheapest/easiest/obtainable.
Carbon pickup is a posibility.
John i have seen these in the power plant i got hurt at it was a 4x4 square with a 1'' hole thru it dont know where they are made but they dont make them at the plant so yes they do make them. Those cermaic tiles sure can put an edge on a knife lol
By tigrooter
Date 02-18-2009 05:26
Edited 02-18-2009 05:46
I was thinking about a drill press set up with a drill bit. just got of the phone with my bud he does some tile with his dad. he said that you can go to a hardware store that sales tile or stone and they make bits that are for drilling holes in tile. he said they cost alot but they last a long time. they have a round head with dimond dust for cutting the hole.
I just use an ole Discarded Cutting or Grinding wheel. Works on all material and the touch-up is minimal