Please excuse the amateur question, but I'm seeking expert advice on troubleshooting the cause of brittle SMAW welds made with a Harbor Freight/Chicago Electric 80 Amp Inverter Arc Welder (
91110).
I'm starting with the assumption that the welder is capable of making good welds (within its limits) based on the product reviews and YouTube videos I've seen, but in my experience I've consistently ended up with brittle welds that basically just fall apart. Often developing a crack as it cools.
Here are some things I've tried:
-Various electrodes:
Chicago Electric 1/16" E6013
Chicago Electric 1/16" E7014
Lincoln Electric 3/32" E6011
Lincoln Electric 3/32" E6013
(Others have reported success using several of these electrode types with this welder.)
-A range of current settings.
-Reversing the polarity.
Supposedly brittle welds can result from oxygen contamination and flux inclusion (
1,
2,
3). These causes would point to bad electrodes. Maybe buying electrodes at Harbor Freight and Lowes (the boxes were pretty dusty at Lowes) is a bad idea, and I'd be better off finding fresher electrodes at a welding supply store, but it seems unlikely that all 4 boxes would have been consistently bad. (I tried a stick or two from each when they were fresh from the store, so I can't blame it on how I stored them.)
Although I've had successful experiences with MIG welding and braising, I am admittedly inexperienced with SMAW and have not spent much time using this welder yet (as clearly can be seen in the embarrassingly ugly weld in the pictures below), so the cause could certainly be my technique, however I'm not producing bad welds just some of the time. It's 100%. I'm finding it hard to see what I could be doing so consistently wrong, especially in light of the dozens of YouTube videos showing this welder being used successfully by amateurs using nothing special for a technique.
Here are some photos of a recent attempt where I tried welding a 1" square tube to a 3/16" plate (using., I think, the Lincoln Electric 3/32" E6013 electrodes). I tried this weld 3 or 4 times, each time using a different electrode type, with essentially identical results.
Here's the stock:
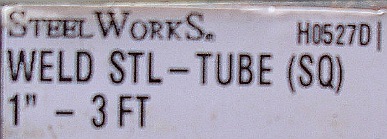
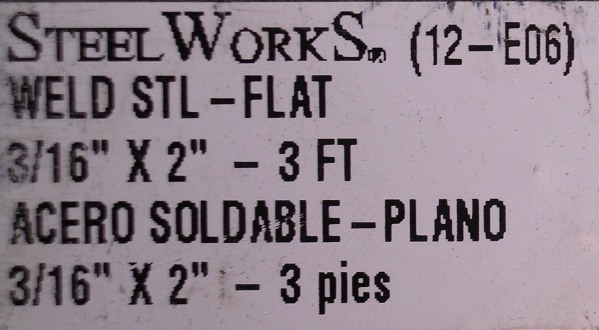
The setup:
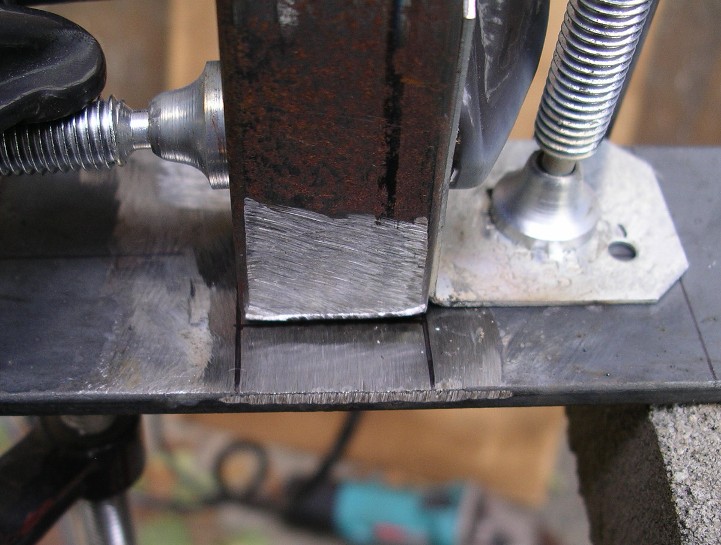
The resulting weld:
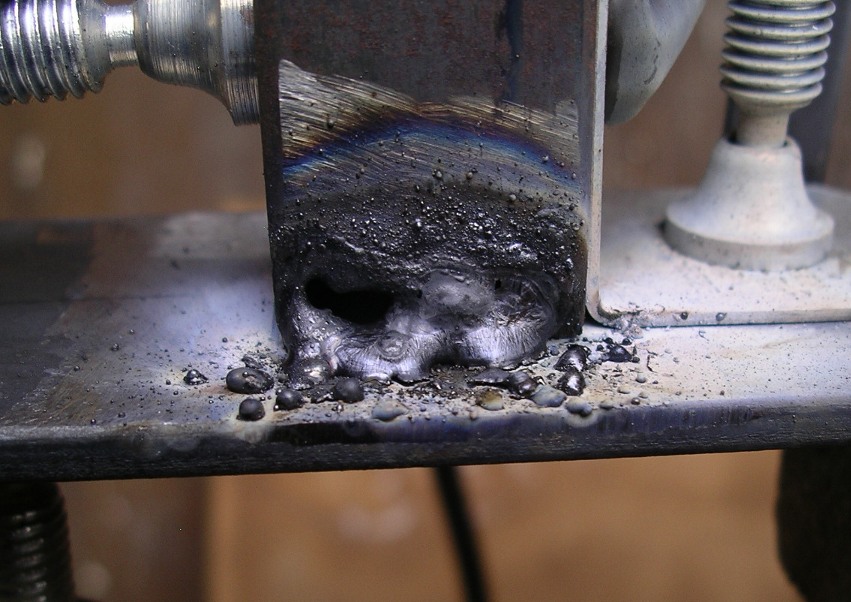
Here you can see a longitudinal crack that formed as it cooled:
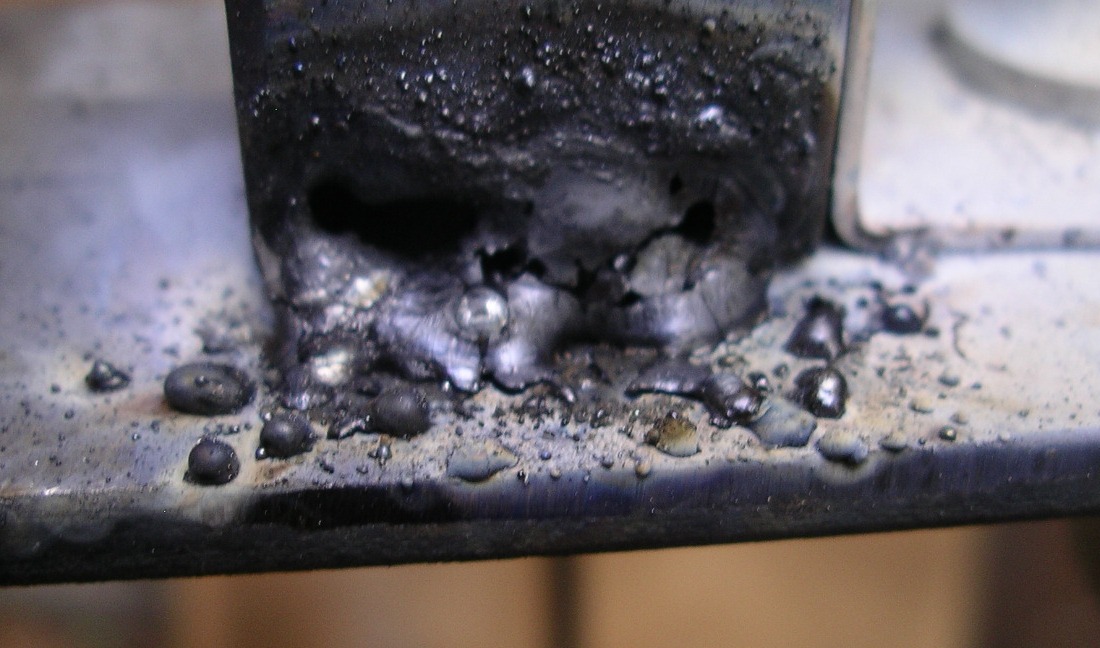
Applying a small amount of pressure and it easily breaks free:
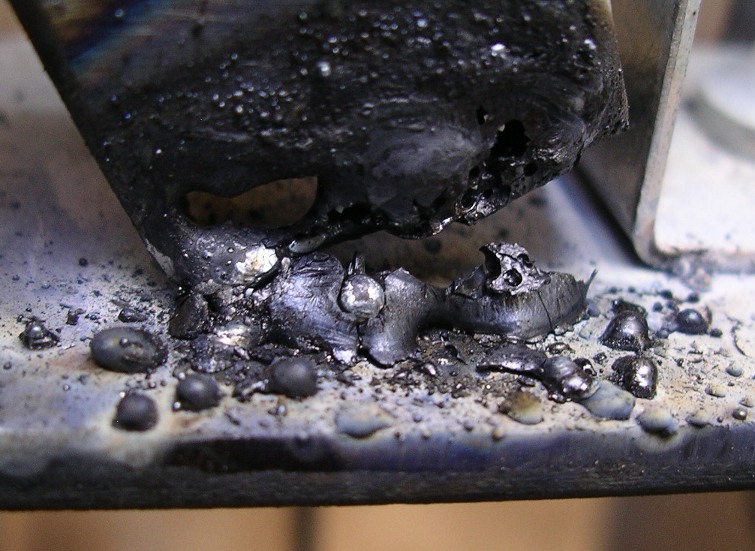
An end view of the tube showing blow through on the left and penetration on the right:
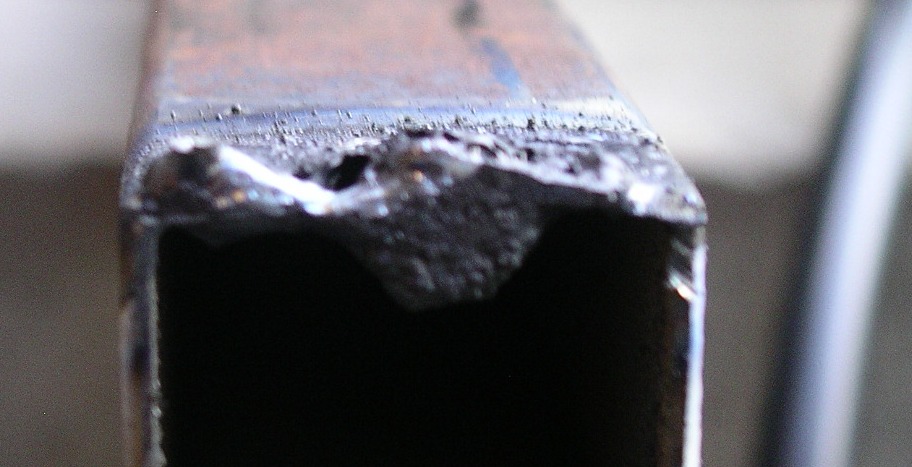
Perhaps chamfering the end of the tube was pointless.
A view of the plate after the slag has been cleaned off. Very little grinding will bring the surface back to what it was before the weld attempt. In this case all but one of the blobs fell off with light grinding, so there's basically no evidence of penetration.
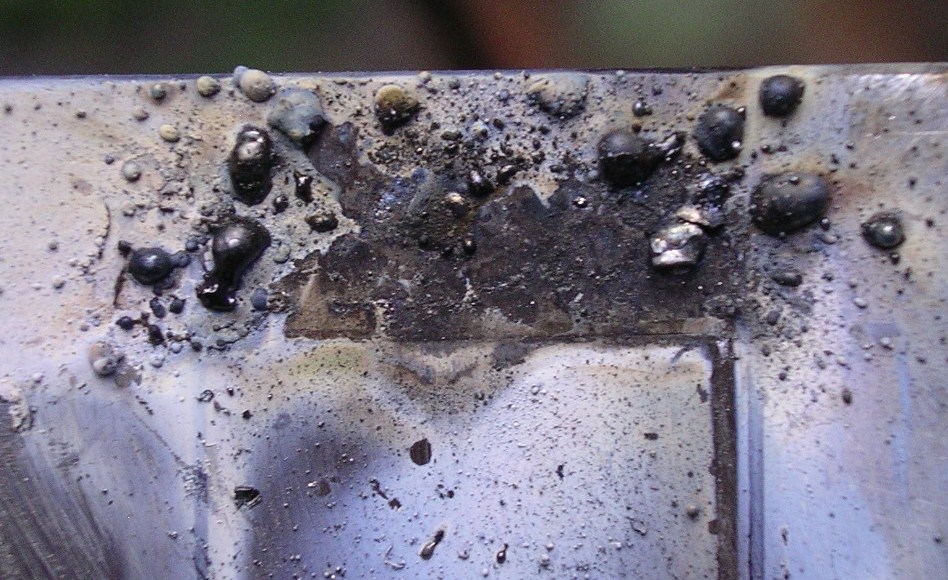
These last few photos illustrate another problem I'm seeing. I'm simultaneously experiencing both blowouts and poor penetration. Blowouts on the vertical piece and almost no penetration on the horizontal piece. Cranking up the current should improve penetration, but it'll also make the blowouts more likely. At least for this problem I'm more inclined to blame my technique.
If the cause of the brittle welds isn't technique, electrode selection, or material, that only leaves the welder itself.
Are there malfunctions in the power source that would explain these results?
-Tom