Hello everyone,
Hope this is a good place to post..
Id like to ask some questions/have someone look over a job im currently working on. Im an entry level welder with only 3yr experience (newb). I wish my job offered better training... its very stressful to basically go from a votech school level and be asked to do something like this without any training or info. So this is a welding inconel by the seat of your pants thread.. hold on!
Me:
99% of what I weld is 304L thinwall tubing. Very little inconel but.. what ive put out up to date is fine.
Filler:
Im GTAW shc10 Inconel 600 to shc10 Inconel 600 and using ERNiCrFe-5 (alloy 62)... ppl at my job weld anything inconel with this stuff.. cast SS to 600, 600 to 600, mild steel to inconel... its the weld all inco at my job. Thats my first question... What do you guys recomend on the 600 to 600 cant seem to find anything on ERNiCrFe-5. I do see alloy 82 is recomended but, whats alloy 62 good for.. could it be everything? Im also welding shc10 Inconel 600 to a .75" 304L flange and found ERNiCrMo-3 (625 filler) is recomended so thats what im using for that.
The app:
This application will go thru extream heat cycles and vibration for long periods of time... I think 300c' to 900C'. Engineers have told me theese are the materials they want to use so im really just looking for the best practice to weld them. If any info is needed to help out please ask.
Sorry if this is hard to read... Im really new to this and just trying to do things right.
I did half today.. and have to admit it was super stressful.
Ill put down the prcedure I do.. maybe some of you could point out things I miss or tips for the next time. I have to build 7 more after this one.
First I built a jig for the thing.. came out nice. This is it with the pipe layed out ready for weld.
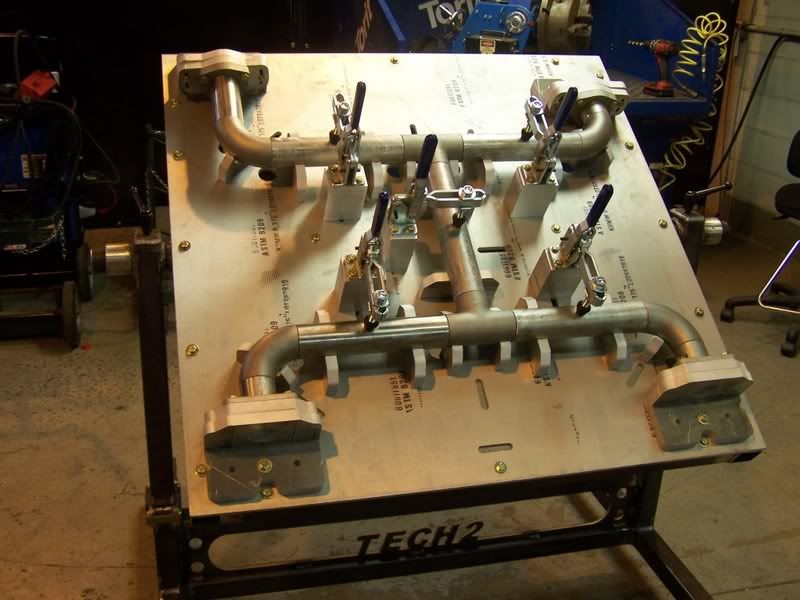
Here are the bevels.. Ive been doing a 30deg bevel leaving around .065 of landing.. Put it in a Simlegreen bath then wire brushed the ends 1" in.
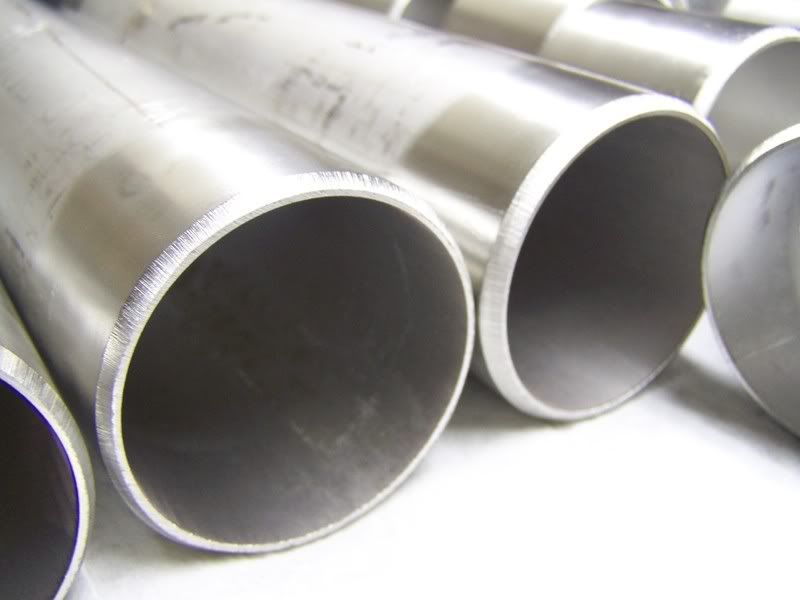
Next put in jig tacked 4 spots then took it to my bench hooked up 1" aluminum plate with purge lines to the flanges..
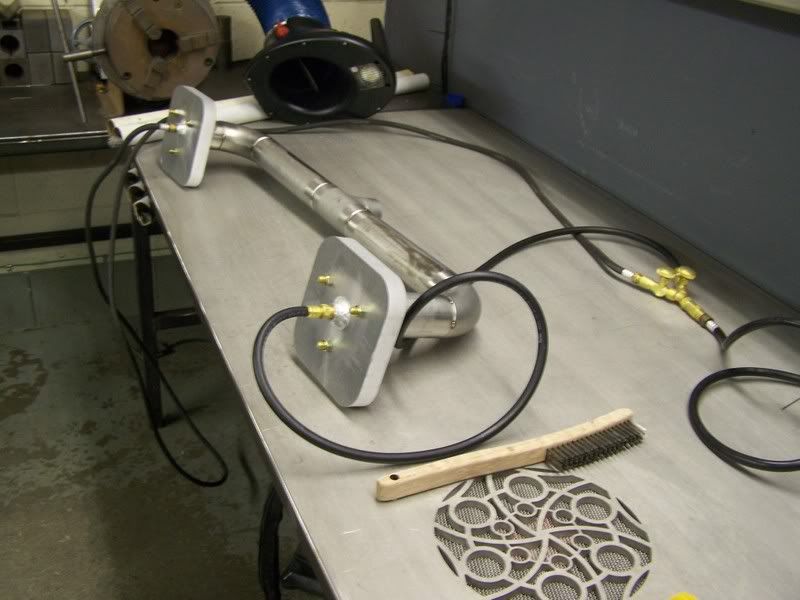
Started welding going 1/4 the way around each joint from one end to the other... checked temp before starting the next run of 1/4 passes with a 250F temple stick.
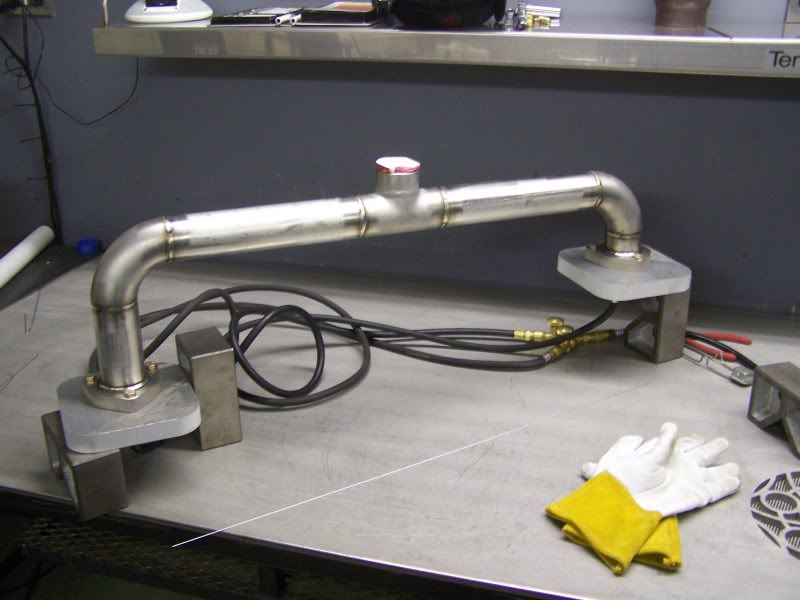
All that seemed ok... I think I could have gone hotter tho. I was pulsing using 150amp main, .9pps,35peak,20backround. Just what worked for me on a test peice.
I had some trouble welding the flanges tho... I noticed I was getting a small crack in the center of the weld. I felt it was because the flange being so thick causing shrink cracking.
I stopped and gave the flange a light pre-heat to 200F... seamed to solve the problem. I did get dark bands in the HAZ area tho.
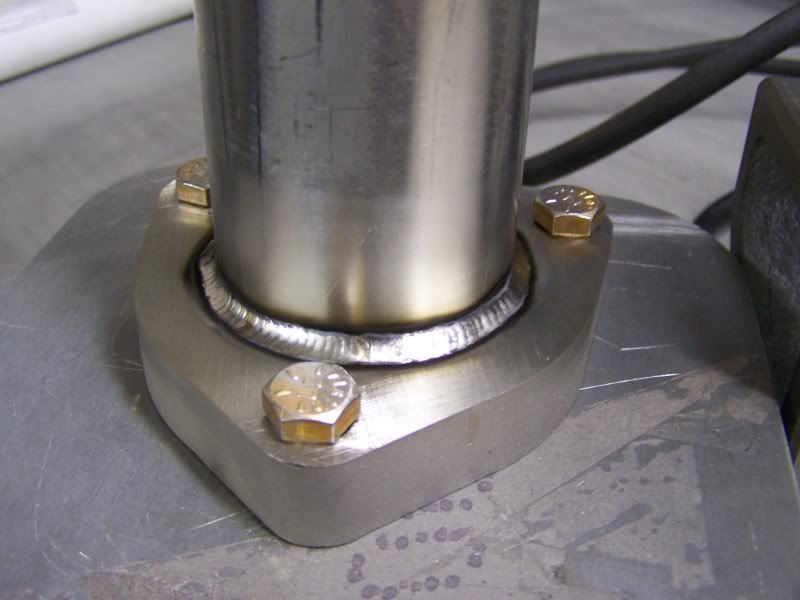
After a light brush
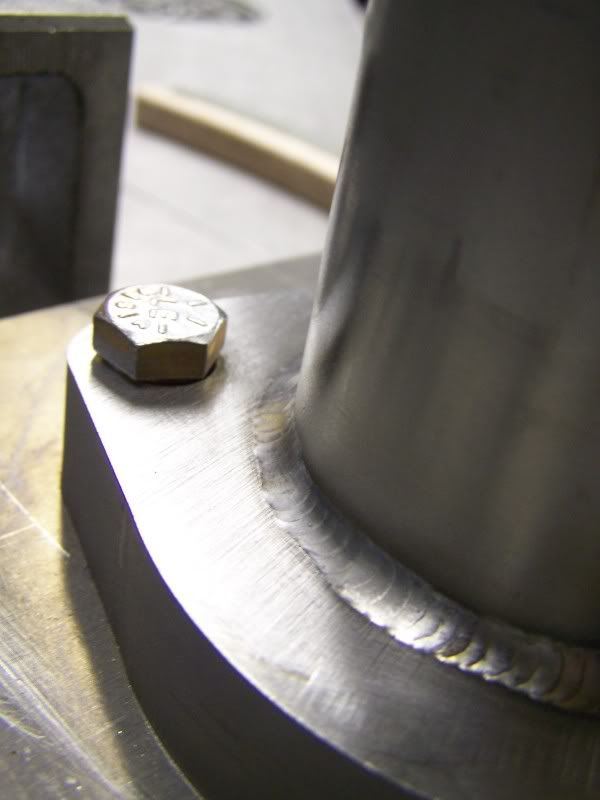
TIA for any help. -Mike