
I might agree with you about the effects of the cutting torch, but that doesn't explain how this tube cracked because it was cut with a band saw,
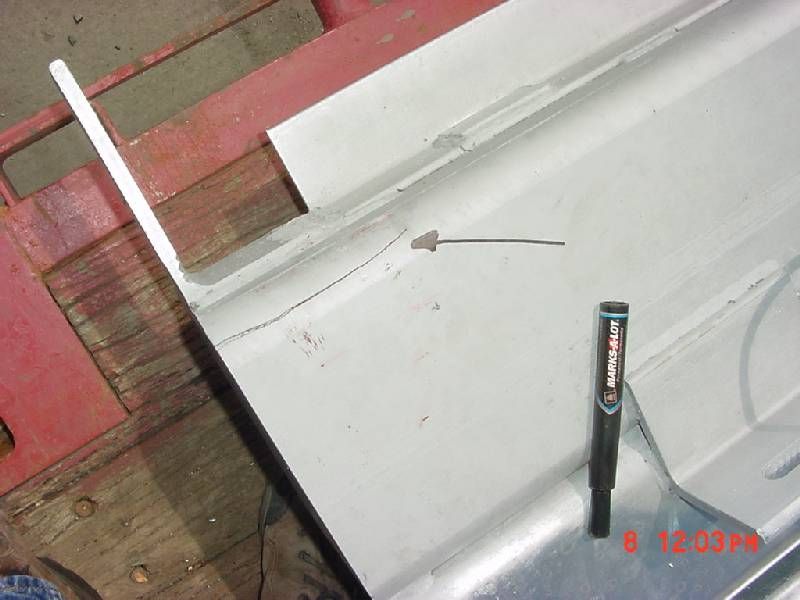
and other trials where we drilled the cope with a drill and sawed back to the drilled hole, sent it off to the galvanizer and that too came back with cope cracks.
When we had galvanized pieces, we tried all sorts of ideas that were thrown out by the AISC, and AGA to try to mitigate this expensive repair work on galvanized pieces.
Here is one that we burned with the torch, ground back to bright material beyond any ill effects that the torch could have produced, yet it came back with cope cracks too.
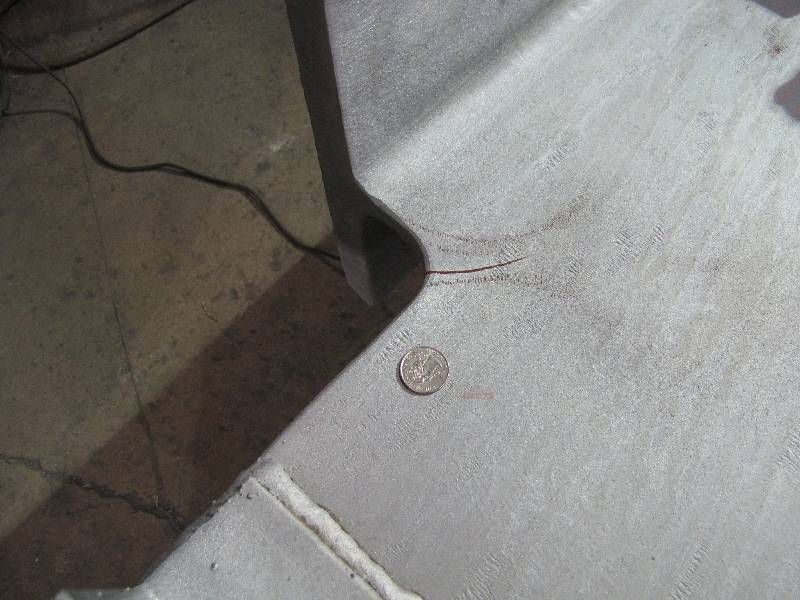
I found that it was only one of several galvanizers that we used where this took place on a regular basis....this was the place that gave me such a fit about the request to see the bath analysis.
I find it funny (actually alarming) that other fabricators were laughing at me because I took the time to bring all galvanized material back and MT (magnetic particle) the usual places where this "cope cracking" happens. They all said they never experienced anything like this, yet none of them ever brought any material back to inspect, so how did they know that their materials were crack free? They all sent the materials straight to the jobsite from the galvanizer and relied purely upon the galvanizer's visual inspection of their materials. As you know Al, many of these indications are not seen with the naked eye, in fact many are covered over and filled in with zinc and until a little magnetism and colored iron powder are applied they are invisible to the naked eye. PT (dye penetrant) won't even find these.
Now I agree with your points to some degree(melting point of zinc 790°F and bismuth 520°F), but with the tin, it can stay fluid longer due to the low melting temp(450°F) and can enter the grain boundaries while the steel is at an elevated temperature, then when the steel cools the grains try to tighten back up as it shrinks, except now it has other elements trapped inside and stresses overcome the material and cracks form. These extra elements are used for wetting and spangle of the galvanized but if used in larger quantities, cracking is more likely. ODOT had contacted me years ago when I expressed my concerns in this forum regarding these problems. They were having the same thing with galvanized bridges and they had found when tin was present in larger percentages in the bath, the cracking was also present.