
Did they give you a welding procedure to weld this coupon out with? If not, they should have...next time when a WPS is not provided ask for one so that you can show them that you know how to use it...and it will give you a range of parameters to set the welding machine. That is a bummer that they left you without much in the way of instructions of what they were looking for out of you.
Just breezing through Lincoln's website and looking at the typical welding parameters for ER70S-3, it looks like for that size wire that you would have to travel pretty quickly or risk burning through 1/4" materials. I hope it had a backing strip and wasn't an open root test...yikes!
Lincoln didn't show the .052 wire with 75/25 shielding, they had the .052 listed with a 90/10 mix which gets you into a spray mode of transfer around 30v and 300-320 WFS using a CTWD of 1/2"-3/4".
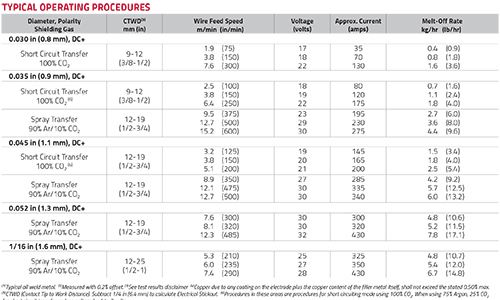
Hard to say what happened as far as the cracking...did they say if it cracked while bending? I'm just wondering what bend radius they may have used and if it was correct for the strength of the material that you welded.